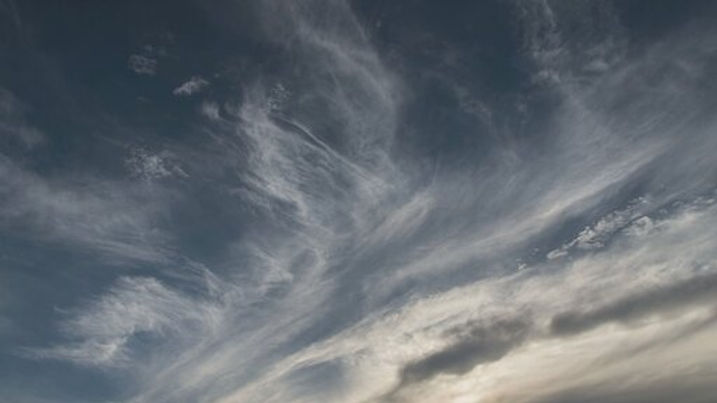

Piezo Accelerometer Tutorial
Accelerometer Design
Assembly of a Vibration Sensor
This video is not supposed to be a real mounting instruction for an accelerometer but it is more to show the basic parts and how they interact with each other. The proper assembly methods have not been explained or mentioned. The parts joining methods must be suitable for the intended environment such as the temperature but also for the vibrating environment. We want to make sure that nothing becomes loose. A common practice is therefore welding or brazing to join the parts. For lower temperatures soft soldering or adhesive bonding may also be suitable. The external housing parts are normally welded together in order to provide a completely hermetic protection and continuous electrical shielding.
We have seen that the time constant (a very important characteristic) is depending on the resistance and the capacity of the piezo element. Regarding the capacity we cannot do much about during the assembly as it is given by design parameters. The resistance however is strongly dependent on the direct environment of the piezo element. It is very sensitive to pollution and humidity.
From this we deduct for the assembly that all the parts must be extremely clean and that there shall be no humidity captured in the housing.
Parts Design
Typical Accelerometer Parts
The details of parts design is of course an important portion of the know-how of a piezoelectric sensors manufacturer. Here we want to look at some detailed considerations which are generally known and published.
The design details of the accelerometer are mostly dictated by the functional intent of the sensor. Shall it be for laboratory use or rough industrial environment, for rather moderate or very high frequencies, for ambient, cryogenic or glowing hot temperatures? The weight is often of prime importance be it to obtain a high resonance frequency or in general not to load the vibrating object unnecessarily.
The first design decision is the choice of the basic functional mode of the accelerometer. Depending on the requirements we will choose normally between compression mode or shear mode or in some cases we would also consider the transverse mode using a flex design.
Base
The prime function of the base is to support the internal sensing element, to allow the mounting of the whole sensor, to support the connector (in most cases) and as a part of the external housing to protect the sensing element from environmental influences. The size and shape of the base will largely determine the weight and the frequency response of the accelerometer.

In our case the requirement for frequency response is moderate. So our design shows four mounting holes right trough the whole block. With a high frequency response requirement a single central mounting stud would have been the preferred option and for an airborne application we would remove all unnecessary material.
However an important feature is the groove around the sensing element. The piezo element is very sensitive to any deformation. You want to decouple it mechanically from deformations of the housing or the mounting surface as good as possible while keeping the transmissibility in the sensing direction. Also the cable may have an influence through the connector to deform the housing and disturb the measurement.
The mounting surface needs to be flat and smooth especially when we intent to measure at high frequencies.
Insulation
We will choose a material which is highly resistive also at the maximum design temperature and which is hard enough to transmit the vibrations. Many of the technical ceramics will normally do the job.
Of course it is much easier to omit any insulation when the electrical layout allows for this.

Piezo Element
In general we look for the piezoelectric material with the highest sensitivity but mostly it is determined by factors like temperature range, temperature response, long term stability and sometimes some exotic requirements like nuclear radiation or other environmental specialties.

Inertial Mass
For the inertial mass we look for a material with a high density so the mass is high (for a high sensitivity) and the volume not too big. Lead would be a good candidate but it is too soft. A simple block of steel or brass would do is but normally we are using a high density material like Tungsten.

All matching surfaces of the sensing element must be flat and smooth in order to transmit the vibration correctly.
Bolt
The preload bolt must be designed to guarantee a sufficient preload under all functional conditions including maximum vibration , shock and temperature over the lifetime of the sensor.
Direct bonding of the parts is a possible assembly variant.
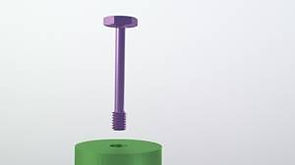
Connector
A hermetically sealed connector (glass or ceramic seal) is recommendable. Again a lot is depending on the required temperature. We have to be aware that the vibration level requirements of our accelerometer is normally much higher than the specification of commercially available connectors. This is the reason that most PE accelerometer manufacturers use often their private design.

It is also important to think about the mating connector. It has to survive and to function in almost the same conditions as the sensor itself. For very rough conditions it is better to avoid the connector at all and foresee an un-detachably integrated cable. This allows to dislocate the connector in a more suitable environment.
Cover
The cover together with the base must provide a hermetic enclosure of the sensing element. At the same time we need a protection from all sorts of mechanical, thermal and electro-magnetic interference. So a rigid metal cover is probably a good choice.
